
#Dynamic response of stack piezo actuators full
This can be as much as 15% of full travel. Another limitation is a significant amount of hysteresis, or variation of travel versus applied voltage between forward and reverse movement. A stack capable of 200 microns of motion (the most common upper limit among commercially available devices) will typically be about 200 mm long. The number of plates grows with increased travel, increasing both stack length and cost as travel increases. Typical piezo stages range in travel from 10 to 200 microns. The most obvious limitation is that of limited travel. Housed piezo stages with internal preload springs are useful positioning actuators, but suffer from several limitations. These limitations can be significantly reduced if the stack is mounted within a housing and if powerful springs are used to produce a high internal preload. Piezo stages by themselves are fragile and unable to produce force in both directions. Depending on the nature of the piezo material (soft versus hard), the applied voltage range is typically either +/- 1000 volts for hard or high voltage stacks, or +/- 120 volts for soft or low voltage stacks. The voltage applied to the piezo stack is distributed to each of the plates within the stack in a parallel configuration. The ratio L/L (change in length to length) for an applied voltage is quite small for a single piezoceramic element, and so most actuators are composed of a large number of thin plates, referred to as a piezo stack. Today, the most common materials used for piezo stages are either barium titanate or PZT (lead zirconate titanate) ceramics. Two design examples are presented which illustrate the effect of the stiffness of the external spring and the size of the design domain on the topology of the solution.The inverse piezoelectric effect was first discovered by Pierre and Jacques Curie in 1881. The optimization problem formulation, finite element implementation, solution algorithm are discussed. In this paper an improved formulation is presented where the piezoelectric properties and stiffness of the stack are included along with an external spring representing a resisting load the actuator is working against. However, it is well known that the best actuator performance occurs when the stiffness of the stack is considered and matches the stiffness of the surrounding coupling structure.

Previously the optimization was done assuming that the stack actuator provided a constant unit load to the compliant mechanism. Two design examples are presented which illustrate the effect of the stiffness of the external spring and the size of the design domain on the topology of the solution.ĪB - A topology optimization method for design of compliant mechanical amplifiers for piezoceramic stack actuators is presented. N2 - A topology optimization method for design of compliant mechanical amplifiers for piezoceramic stack actuators is presented.
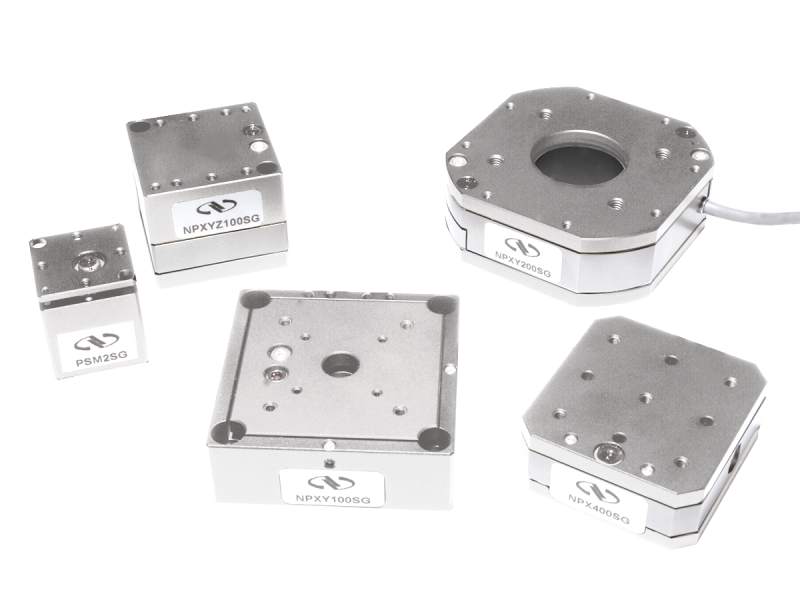
The authors gratefully acknowledge the support of National Science Foundation Division of Design, Manufacture, and Industrial Innovation grant number DMI-9870527. T1 - Design of compliant mechanical amplifiers for piezoceramic stack actuators considering stiffness properties
